Duplex and lean duplex, the high-strength, 100% recyclable stainless steel grades, are becoming popular in support and load-bearing structures, thanks to their features such as corrosion resistance, light weight, energy absorption capacity and low life cycle costs. In this blog, we discuss duplex and lean duplex as materials: their development, chemical composition and mechanical properties. Next week, we will walk you through how to use them in practice, covering topics such as cutting, bending, welding and drilling.
There are many ways and reasons to use duplex and lean duplex. The oil and gas industry benefits from their durability and corrosion resistance in the topsides of platforms located in harsh conditions, the transportation industry can manufacture light, strong and safe bus bodies, the building and construction industry uses them in demanding environments like bridges and dams, and the process industries make use of the hygiene and resistance to stress corrosion cracking – to name just a few.
In a recent webinar organized for the bus building industry, 57.9 % of participants said they will consider lean duplex as part of their bus body structure in upcoming projects, 71 % of them being currently aluminum or carbon steel users.
Over the years we have delivered duplex and lean duplex hollow sections and profiles for various applications all over the globe, and you might spot our products on one of the largest oil fields in the North Sea, in floodgates located in the middle of a national heritage landscape or in thousands of buses on 6 continents.
We have seen a growing trend in choosing these stainless steel grades over mild steel or austenitic stainless steels. In some markets in the oil and gas industry we are now providing a greater share of duplex than Austenitic 316L.
In a recent webinar organized for the bus building industry, 57.9 % of participants said they will consider lean duplex as part of their bus body structure in upcoming projects, 71 % of them being currently aluminum or carbon steel users.
As the interest in these materials has been evident, we set out to create a couple of blogs focused on different aspects of duplex and lean duplex. In this first post, you will read about duplex and lean duplex as materials. In the next one, the focus will be on practical matters: things to consider when cutting, bending, welding and drilling duplex and lean duplex.
Let’s get started – what is Duplex?
Duplex is a stainless steel material made of austenite and ferrite grains, an approximately 50/50 share of each. The name duplex actually comes from this two-phase microstructure. The combination of the hard ferrite and tough austenite creates attractive properties unlike those of mild steel or ferritic or austenitic stainless steels alone.
A brief history of Duplex
Duplex stainless steels are not a new invention – in fact, they have been used for over 100 years. The weldability of those early duplex materials was not extremely good, and in the beginning, they were mainly used in castings. The reason for their adoption in castings was to avoid hot cracking, as austenitic stainless steels were prone to it, whereas duplex grades are not.
The oil and gas industry was an early adopter of duplex stainless steels, and for a long time, most of the structures made of duplex were indeed sold for this particular market.
In the 1970’s, thanks to improvements made in the steel refining process, it became more common to use duplex in other applications besides castings. The first commonly recognized duplex grade, 2205 (EN 1.4462, S32205) was established, and it is still today the most used duplex grade globally.
As kind of a “standard” duplex grade it is used in structures not just by the oil and gas industry but also industries such as pulp and paper and the construction industry.
It has proven to be a strong performer in applications needing high strength, good corrosion resistance and good resistance to stress corrosion cracking. The latter is a benefit provided by the ferrite grains of the material, making 2205 highly useful in environments where chlorides, humidity or elevated temperatures can cause stress corrosion cracking (and where, due to this, austenitic grades might not do the job).
After the development of 2205, more duplex grades have been brought to the market. These are often called super duplex grades due to their improved corrosion resistance.They include a group of lean duplex grades that were developed to replace common austenitic grades such as 304 and 316 that have a high nickel content of circa 8-11 %. By decreasing the nickel content to ~1.5-4 %, the aim was to provide a material not affected by the fluctuating, at times high, nickel prices.
The weldability is also good in these modern grades, such as EN 1.4062 (DX 2202), EN 1.4162 (LDX 2101) and EN 1.4362 (EDX 2304).
Mechanical properties of Duplex and Lean Duplex
Due to their two-phase microstructure, duplex and lean duplex grades have a considerably higher yield strength than austenitic and ferritic stainless steels or carbon steel – they are generally twice as strong.
Their toughness and elongation exceed that of ferritic grades, and the combination of high strength and good elongation results in an excellent energy absorption capacity.
This is quite ideal for applications such as bridges and rollover structures of bus bodies.
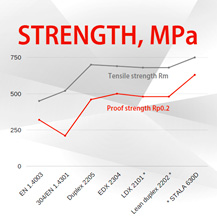
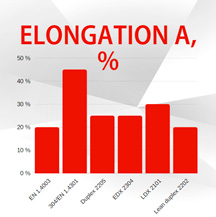
* Lean duplex grades 2101 and 2202 can be further strengthened with our strength class STALA 630D, giving them a yield strength of 630 MPa.
To read more specifically about the strength and elongation of hollow sections made of lean duplex 2202 and strength class Stala 630D, find a blog about their testing here.
Resistance to corrosion and stress corrosion cracking
As for corrosion resistance, duplex and lean duplex grades are generally comparable to austenitic grades, outperforming the corrosion resistance of ferritic grades.